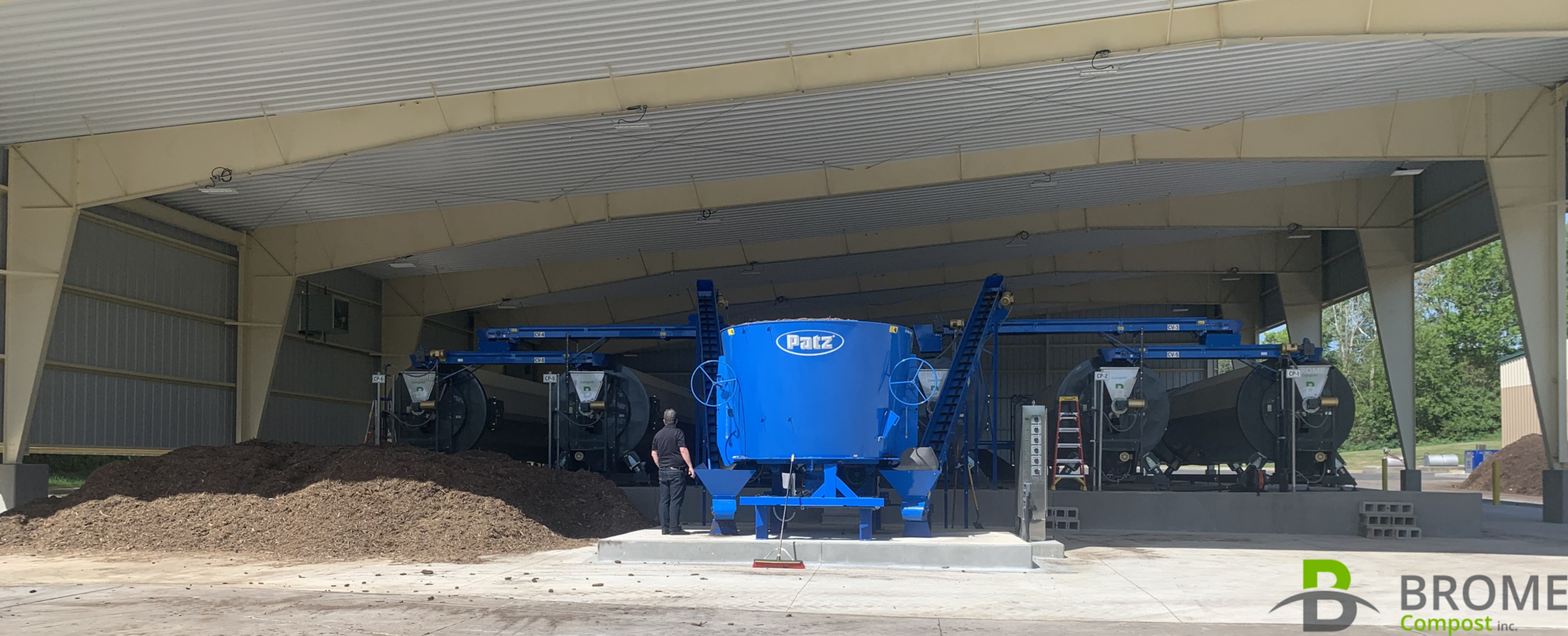
At over 2500 metric tons, the on-site industrial composting system installed for the City of Bentonville in Arkansas is one of the largest ever created by the Brome Compost team. Needless to say, we are more than a little proud.
Bentonville’s industrial composting site is designed to handle the city’s biosolid waste, turning what is essentially sewage sludge into usable compost. The term biosolids refers to the nutrient-rich, organic matter resulting from the final stage of a municipality’s wastewater treatment process. Rather than simply disposing of it, biosolids can be a beneficial resource and used as a high quality soil amendment.
The benefits of an on-site industrial composting system for managing biosolids
With landfill and incineration no longer a viable option for managing its biosolids, the city was looking for ways to minimize some of the challenges associated with its traditional windrow composting site. These include the additional labor costs incurred from manually and mechanically rotating the windrows, as well as the large surface area needed for a project of this scale. In addition, a made to measure industrial composting system allows for better control of the composting process, with less need for bulking agents and less risk associated with odor management and leachate.
Another goal for a municipality could be to improve industrial symbiosis, with the bulking agents needed to compost the biosolids potentially coming from a variety of sources. Carbon rich bulking agents can include wood shavings, corrugated cardboard, and shredded paper. By sourcing these from local sources, the waste from one business or economic sector can become a valuable resource for another: the very principles of a circular economy!
A made-to-measure composting system to perfectly meet Bentonville’s needs
The on-site composting system designed for the City of Bentonville is made to handle more than 20 tons of biosolid matter a week and consists of 6 Brome 632 rotating composters, which are automatically fed by an industrial mixer and an arrangement of conveyor belts. The use of a mixer optimizes the composting process as it helps homogenize the material to be composted while also reducing its volume. Once the biosolids have passed through the composting system and come out on the other side as compost, another set of conveyor belts moves it towards a pile where it is collected for the maturation process.
Have a look at this video to see an overview of the composting site:
The three major objectives for Bentonville’s new system were:
- Renovate an existing composting site
- Reduce the site’s footprint
- Radically reduce odor problems
To learn more about the benefits of industrial scale composting for municipalities, please see our page Composting for Municipalities